This rotator has its good and bad points, and hams certainly have opinions! However, like any piece of equipment it is important to understand its capabilities and limitations and only use it accordingly. It won't survive when tasked with turning the largest HF yagis and large stacks, but it is certainly good for mid-size arrays.
In this article I'll point out only some of the points of the overhaul process that I believe are worth describing. There are many other descriptions of the full overhaul process out there, and even some videos, so there is no need for me to do it.
Signs of trouble
I purchased the rotator fully aware that it needed an overhaul. It was poorly stored, possibly sitting outside on the ground for a while, and it showed on the outside. Since the terminal strip was badly rusted I replaced the 8 terminal screws and scraped off some of the corrosion. When I first connected the cable and turned it on it did turn, although grudgingly. Clearly the bearings were not in good shape. Since I was terribly busy with the pending move I put the rotator aside until later.
That time is now since I intend it for the Trylon tower where it will turn a couple of mid-size yagis. One evening during the early stages of tower construction I opened the rotator and was presented with a real mess.
All the balls on the bottom bearing were badly rusted. This bearing is effectively the weather seal in the gap between the rotating and static parts of the rotator. There were even signs of rust on the upper bearings. I tossed the lot of them and the ring gear into a vat of solvent. I let them soak for a couple of hours, with periodic agitation, while I cleaned the lower half of the rotator's innards. The upper half of the rotator (above the top bearing) was surprisingly clean and needed little attention.
When I pulled the parts from the solvent bath I was able to separate the balls from the plastic retainers without damaging the retainers to which the balls had been firmly attached. Vigourous brushing of the retainers removed the rust particles and dirty grease that remained. The balls of the lower race were barely recognizable as ball bearings: they were not at all spherical, plus they were completely rusted and deeply pitted.
Most of the balls in the upper bearings passed inspection. A ball that showed the smallest evidence of pitting or rust was discarded. Balls are cheap so don't develop an emotional attachment to these bits of metal. Otherwise you'll pay a higher price, later.
Inspection: what to look for
Here's a quick list of things I look for when inspecting Hy-gain rotators. Since my list is similar to that of others I won't spend much time on it.
- Ring gear: Look for pitting, chipped or broken teeth and metal spurs. Most defects cannot be fixed so you'll have to purchase a replacement. This is not uncommon.
- Brake teeth in the bottom housing: There should be no broken or heavily worn teeth. If you have much of this consider replacing the rotator since it's been heavily used and abused over the years.
- Bearing races: Check all surfaces for deep indentations or fretting damage. Again, there is little that can be done here except replacing the rotator. If you try to sand the races you'll only introduce slop in the bearings and accelerate further damage. You can continue to use the rotator with some race damage but plan for replacement.
- Brake solenoid and wedge: Look for deep scoring in the wedge's front and sides, and the solenoid housing where the wedge slides through. Consider replacing the brake since there is excess play that will accelerate further deterioration and eventual failure. That will damage transmission lines and could damage the antennas when the brake fails. Also inspect the return spring and replace as necessary. Operate the brake a few times with the rotator open and watch its action.
- Reduction drive: Test for slop and tooth wear in the spur gears.
- Indicator pot: The top surface of the windings should be clean and shiny with no evidence of wire abrasion. The wiper tension should be sufficient to press firmly against the winding at its lowest point. The tangs on top of the wiper must be symmetric and straight. Look inside the bell housing to check for abrasion of the tabs that engage the wiper. It's only aluminum and will wear over time can eventually fail to hold the wiper. Yes, this really does happen.
Replacement ball bearings

Hy-gain itself doesn't say. So I'll say it:
T2X and Ham series ball bearings are ⅜"Happily these are easy to find at any industrial bearing shop. They are half the price by mail order (Hy-gain sells replacement bearing kits as well) but I was not willing to wait the typical 2 week delivery time. Much to my surprise the bearing shop had only 38 in stock when I stopped by. They had thousands of other sizes but not ⅜".
Since this was Ottawa, where I no longer live, and could not easily drop by the next day to pick them up they offered to courier them to me for a nominal fee. Two days later 300 ball bearings arrived at my front door. About 70 of them went into the T2X. The rest are being stored for future Hy-gain rotator overhaul projects.
Cleaning it up
I was mostly concerned with loose debris and caked on dirt/grease on the bearing races. The former was removed with a small brush and a blower while the latter was removed with a rag dipped in solvent. The spur gears, motor and indicator pot were very clean and properly greased so I left them alone.
After cleaning the races with solvent I used steel wool to carefully remove any remaining debris until the races were clear and smooth. I tested by running a finger along the full circumference of both faces of every race. There was little evidence of fretting or undulations. The rust stains from the ruined ball bearings on the lower race required additional cleaning with the steel wool until they passed the finger test.
![]() |
All cleaned up and ready for a fresh coat of grease |
The remaining discolouration of the cast aluminum is not a concern. Do not keep sanding until it is shiny since that serves no purpose and can degrade the race. Do not use an abrasive stronger than soft steel wool, and even then use it lightly and sparingly. Avoid using sandpaper with a grit coarser than 1000.
Grease
Many types of grease are suitable for these rotators. White lithium grease is the one I use most often since it is easy to work with, is inexpensive and has decent all-season performance. This time I decided to try a synthetic grease for reliable performance in our frigid winters and adhesion out in the summer sun. We'll see how the experiment goes. Others report good results.
You do not need to use a lot of grease. Too much and it will be squeezed out during operation and possibly foul other components and bog down the reduction drive.
With your finger (use a plastic glove to keep yourself tidy) spread a thin layer of grease on the bottom and inner and outer edges of the ring gear and the flat surface on which it sits. Don't grease the top of the ring gear since it is affixed to the bell housing.
Do the same for all the bearing races. There are 6 race surfaces in the T2X, two for each for the 3 bearings. I like to also add a thin layer of grease directly to the ball bearings after they've been inserted into the retainers, but this is not strictly necessary. Be sure that if you do that the total amount of grease is not excessive. There should not be visible globs of grease anywhere.
Putting it back together

In the picture at right the main body of the rotator is in proper configuration for attachment of the bell housing. There are 3 steps to get to this point:
- Turn the rotator in either direction until the limit switch cuts off the motor; I chose clockwise, as seen from above. This step positions the ring gear.
- Turn the wiper on the indicator pot by hand to the stop in the same direction you just turned the rotator.
- Install the upper bearing. The grease should keep it from sliding off.

Now tilt the bell housing and you'll notice that all the ring gear tabs are approximately directly overhead those 3 protrusions on the ring gear. Pick one for reference and make a mark on the outside of the bell housing at the tab's centre. Use a felt marker or a bit of tape. This step is important since you must install the bell housing blind; that is, you can't directly see the hooks and tabs.
Gently lower the bell housing over the rotator body until it is an inch above the ring gear. Visually align the mark and the ring gear protrusion and, keeping the bell housing vertical and centred, lower it until it contacts the ring gear. You should only have to rotate the bell housing a tinyamount for the tabs to seat against the ring gear. If you've done this right the pot will also have properly engaged its tabs.
To test if the pot is properly seated run the rotator away from the stop for perhaps 10 degrees. You should see the indicator on the control box move with the rotation almost immediately. If not you should suspect a problem. Now rotate it back towards the stop. There should be no hesitation before the indicator moves. If the pot is not properly engaged it may take a second or two before the indicator shows movement.
If you got it right do a full rotation to the other stop and back again to whatever direction you wish for installation on the tower. Otherwise take the bell housing off and try again. Do not keep playing with rotation if the symptoms I mentioned are evident since you are likely to damage the pot wiper. As often as I've done this I still managed to get it wrong with this T2X. I was successful on the second attempt.
With the hardest part out of the way we are close to completing reassembly. There is only one special trick left to do.
Turn the rotator upside down, taking care to keep the bell housing firmly seated against the rotator body. You really don't want to do the alignment procedure over again, do you? Install the remaining two bearings on the rotator body.
If you have a quick disconnect plug on the rotator (all recent model T2X have a plug rather than a terminal strip, but not mine, alas) unplug it, or disconnect the wires from the terminal strip if that's what you have. Thread the cable through the bottom half of the housing and reattach the cable. We need to operate the rotator for the next step.
Lift the lower housing and position it over the rotator body. Lower it carefully, ensuring that it is vertical and centred. You will likely hit resistance when the lower housing contacts the brake wedge. You can drop it further if you position the brake wedge between two teeth, but don't do it this way since the housing will not be centred. The reason is that the spring forcefully extends the brake wedge further than the diameter of the lower housing. Don't fight with it: the solenoid spring is quite strong and you'll knock the bearings off the races.
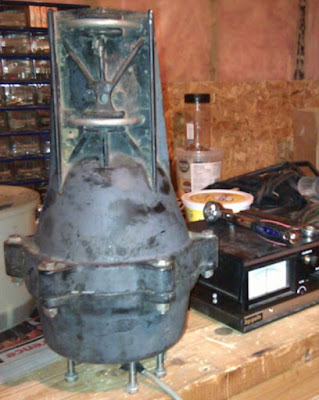
I suggest doing this only finger tight and testing the rotator for full rotation. Only then would I tighten the bolts. Do not tighten the bolts in sequence; as one tightens move to one approximately opposite to it, to avoid higher stress on one side of the rotator. Admittedly the risk is low but why not when it's easy to do.
Done
As you can see I made only a perfunctory attempt to clean the rotator exterior . Its appearance is of no interest to me; I only care about the inside. Some hams like to make them nice and shiny and will even give them a new coat of paint. Do whatever moves you.
While it isn't clear in the photo the indicator is calibrated and set to point north, which is the rotation centre. That direction is convenient for setting the yagis correctly and for adjusting the length and position of the rotation (drip) loops in the transmission lines.
Now all that's left is to install it on the tower. But first I have to complete the tower. Weather and the holidays are making that difficult for the present. One of my friends told me not to worry about it too much since the bands are so lousy. We'll see.
Merry Christmas or whatever holiday you choose to celebrate.